Mr. To Hoai Nam - Permanent Vice President, General Secretary of the Vietnam Association of Small and Medium Enterprises, stated that the application of digital technology and automation is inevitable, especially in the new era, the era of national development. According to Mr. Nam, this not only helps businesses increase productivity, improve product quality, save natural resources but is also an important pillar towards sustainable development.
From the business perspective, Mr. Huynh Tan Quyen - Deputy General Director of CADI-SUN shared that the business always takes productivity and quality as a measure for the product. Therefore, since the early years of establishment, CADI-SUN has continuously sent staff to study productivity-increasing models in advanced countries to apply to its factories and production lines.
According to Mr. Quyen, thanks to the high determination of the management board in improving productivity, the enterprise has solved the problem of improving product quality. CADI-SUN has greatly improved its production technology. From factories, workshops, technological equipment lines are invested synchronously from advanced countries in the world to produce electric cables.
“We realize that to do this, we must have strong and large enough financial resources to invest; there must be high determination from leaders to workers in improving and innovating. Because no matter what, improvement and change will affect old habits and old ways of doing things... so we need to have a breakthrough determination (especially in improving the application of software and 4.0 technology into production and business),” said Mr. Quyen.
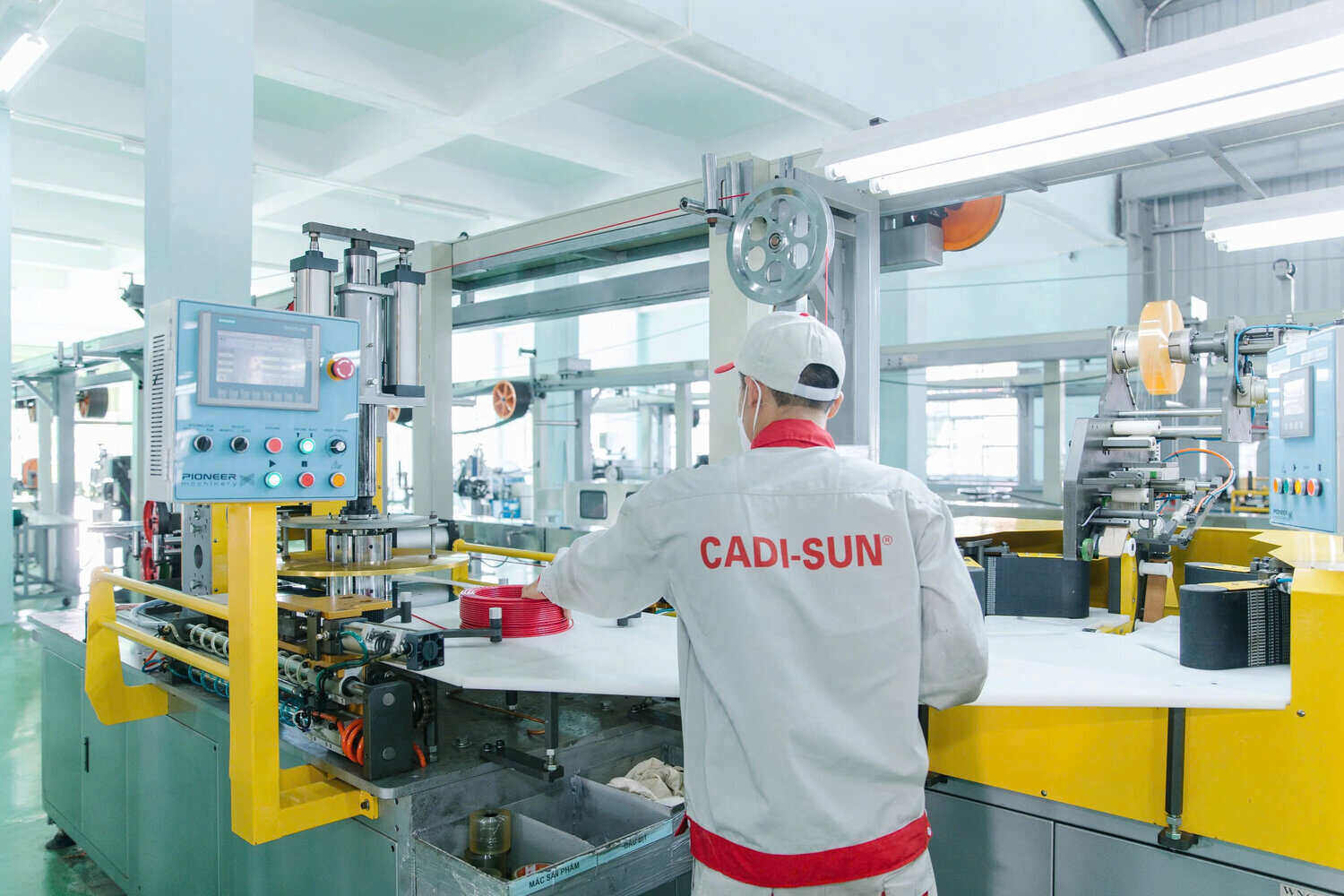
From the perspective of a productivity expert, Mr. Le Minh Tam - Director of the Center for Training in Standards and Quality Measurement, National Standards and Quality Measurement Committee said that to increase productivity, businesses need to pay attention to 4 criteria. First, leadership commitment: leaders must understand, desire/desire and commit to actions, specifically investing resources (correct and sufficient), effort and time for this production improvement. Leaders also need to create a mechanism to encourage process improvement, have a policy to recognize and reward the achievements of improvement. At the same time, promote process improvement as part of daily work (not as extra work).
Second, the approach must be systematic, with a long-term vision. When first implementing, it can be implemented on a small scale and scope to ensure that the appropriate approach is found for the organization (suitable for the organization's specific capacity, personnel, and culture).
Third, seriously invest in learning/training to truly understand how to do things, methods, techniques and tools for process improvement. Specific knowledge and skills such as process analysis, problem identification, problem solving... with cycles such as PDCA, DMAIC... or QC tools (7 old tools, 7 new tools), project selection and evaluation, data collection and analysis... all need to be learned to master them. Only then can the personnel implementing process improvement work effectively.
Fourth, process improvement can start with detected nonconformities (NC) (this is the common way), or start with opportunities for improvement (OFI).